在现代汽车的研发过程中,减轻车身重量一直是工程师们关注的重点之一。其中,底盘的轻量化尤为关键,因为它不仅关系到车辆的操控性能和舒适度,还直接影响着燃油经济性和安全性。本文将深入探讨底盘轻量化的技术原理及其在实际应用中的挑战与解决方案。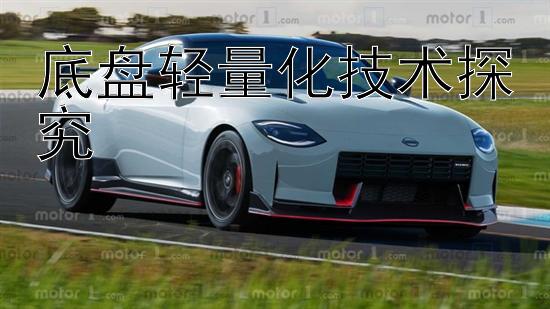
什么是底盘轻量化?
底盘轻量化是指通过使用更轻的材料或优化结构设计来降低车辆底盘系统的整体质量。传统上,钢材料由于其强度和高性价比被广泛应用于制造汽车底盘部件,但随着技术的进步和对节能减排要求的提高,铝合金、镁合金以及碳纤维复合材料等新型材料逐渐崭露头角。这些新材料具有密度低、比强度高的特点,能够显著减少零部件的重量,从而达到轻量化的目的。
底盘轻量化的好处
- 油耗降低:减轻了车重意味着发动机所需的动力减小,可以有效提升车辆的燃油效率,节省能源消耗。
- 加速性能提升:轻量化后,车辆启动加速所需的时间缩短,响应更加迅速。
- 制动距离缩短:较轻的车身使得制动的负担减轻,有助于缩短刹车距离,提高行车安全。
- 操纵稳定性增强:减轻了底盘负担的车辆转向更加灵敏,操控性更好,驾驶体验得到提升。
- 碰撞安全性改善:虽然减轻了重量,但通过合理的设计,仍然能确保甚至提高车辆在发生事故时的被动安全性。
实现底盘轻量化的技术手段
- 材料替换:采用高强度的铝合金代替传统的钢材制作悬挂系统组件、副车架等部件;或者利用碳纤维增强塑料(CFRP)制造传动轴、引擎盖等零件。
- 结构优化:通过计算机辅助设计和有限元分析(FEA)等方式优化底盘的结构设计,减少冗余材料的使用,同时保持结构的刚度和强度。
- 连接工艺创新:激光焊接、铆接、胶粘剂等新技术可以在保证连接强度的前提下进一步减轻连接部位的重量。
- 生产流程改进:引入自动化生产线和先进的生产设备,提高生产效率的同时也能减少不必要的材料浪费。
面临的挑战及解决办法
- 成本控制:新材料的采购价格通常较高,且加工难度也很大,因此如何在保证品质的前提下降低成本是工程师必须考虑的问题。可以通过大规模生产和供应链管理来实现成本的节约。
- 耐久性与可靠性:减轻后的底盘部件可能面临长期使用过程中的疲劳问题和耐腐蚀性考验。这就要求在设计阶段充分考虑到材料的特性和环境因素的影响,并通过严格的测试程序来验证产品的寿命。
- 维修便利性:当发生事故时,如何快速有效地修复轻量化材料制成的零部件也是一个难题。针对这一点,制造商需要制定专门的维修指导手册和技术培训计划,以帮助维修人员掌握相关技能。
综上所述,底盘轻量化技术不仅是未来汽车发展的趋势,也是应对日益严苛的环境法规和消费者需求的必然选择。随着科技的不断进步和产业链的成熟,相信这一领域将会涌现出更多创新成果,为人们带来更加环保、高效和安全的新一代交通工具。